Snack Packaging Machines: Efficiency, Innovation, and Future Trends
- The Importance of Snack Packaging Machines
- Core Components of Snack Packaging Machines
- Hopper System
- Conveyor Belt or Feed Mechanism
- Weighing System
- Form-Fill-Seal (FFS) Unit
- Sealing Mechanisms
- Cutting Unit
- Printing and Labeling Module
- Discharge and Collection System
- Advanced Features in Modern Snack Packaging Machines
- Customization for Different Snack Types
- Maintenance and Operational Insights
- Applications and Benefits
- Applications
- Benefits
- Future Trends in Snack Packaging
- Conclusion
Snack packaging machines play a vital role in modern food production, ensuring freshness, hygiene, and efficiency. From hoppers and weighing systems to sealing and labeling units, these machines streamline operations, reduce waste, and boost scalability while meeting global safety standards.
In today’s competitive snack market, packaging is no longer just a protective layer—it is a key factor in extending shelf life, preserving freshness, and attracting consumers. Modern snack packaging machines have revolutionized the food industry by delivering automation, accuracy, and sanitation. These advanced systems ensure efficiency, consistency, and compliance with international safety standards while reducing dependency on manual labor.
The Importance of Snack Packaging Machines
Snack packaging machines have transformed how products are prepared and delivered. Automation addresses critical production challenges such as high-speed operations, reduced material waste, and contamination prevention. By ensuring scalability and uniformity, these machines enhance efficiency while maintaining strict quality control.
Moreover, automated systems improve hygiene and reduce human error, optimizing resource utilization, lowering costs, and boosting customer satisfaction.
Core Components of Snack Packaging Machines
Hopper System
The hopper serves as the entry point for snacks, ensuring smooth and consistent product flow. Depending on snack type, systems may include single or multi-hoppers for better handling of different product shapes and sizes.
Conveyor Belt or Feed Mechanism
The conveyor system transports snacks efficiently through the packaging line, with adjustable speeds to prevent bottlenecks during large-scale production.
Weighing System
Most modern snack lines use multihead weighers for precise portioning. This technology minimizes waste, improves accuracy, and ensures consistent product weights.
Form-Fill-Seal (FFS) Unit
The FFS system forms the packaging material, fills it with product, and seals it. Vertical FFS is commonly used for snacks, while horizontal FFS is suited for delicate or irregularly shaped foods.
Sealing Mechanisms
Sealing ensures airtight packaging and longer shelf life. Options include heat sealing, ultrasonic sealing for heat-sensitive snacks, and adhesive sealing.
Cutting Unit
Packages are cut to size with straight or serrated edges, ensuring professional appearance and brand consistency.
Printing and Labeling Module
Modern machines integrate printing and labeling, allowing batch codes, expiration dates, and QR codes for traceability and compliance.
Discharge and Collection System
This unit delivers finished packages smoothly to storage or shipping, preventing workflow interruptions.
Advanced Features in Modern Snack Packaging Machines
Today’s snack packaging machines incorporate smart technologies such as real-time monitoring, automatic adjustments, and diagnostic systems. They support eco-friendly packaging solutions, enabling the use of recyclable and biodegradable materials to meet environmental standards.
Customization for Different Snack Types
-
Dry Snacks (chips, nuts, popcorn): Moisture-resistant packaging
-
Powdered Snacks (seasonings, spice sachets): Airtight portioning
-
Sticky Snacks (gummies, candies): Non-stick and hygienic coating
-
Fragile Snacks (crackers, baked goods): Gentle handling to prevent breakage
Maintenance and Operational Insights
Routine maintenance—cleaning, lubrication, and alignment checks—is essential for consistent performance. Operator training reduces downtime and ensures efficient handling of common issues such as hopper blockages or sealing failures.
Applications and Benefits
Applications
-
Large-Scale Production: Automated systems streamline high-volume snack manufacturing.
-
Small-Batch Production: Flexible designs benefit custom snack producers.
Benefits
-
Cost reduction through lower labor and material waste
-
Improved product quality and freshness
-
Scalability to meet growing production needs
Future Trends in Snack Packaging
The future of snack packaging machinery is being shaped by:
-
AI-driven automation for predictive maintenance and optimization
-
Sustainable packaging materials to minimize environmental impact
-
Enhanced food safety features to meet demand for allergen-free and organic snacks
Conclusion
Snack packaging machines are at the heart of modern snack production, combining precision, efficiency, and hygiene. From hoppers to labeling systems, every component contributes to freshness, consistency, and customer appeal. As technology evolves, these machines will continue to set new standards in food packaging automation, ensuring snacks reach consumers fresh, safe, and attractively packaged.
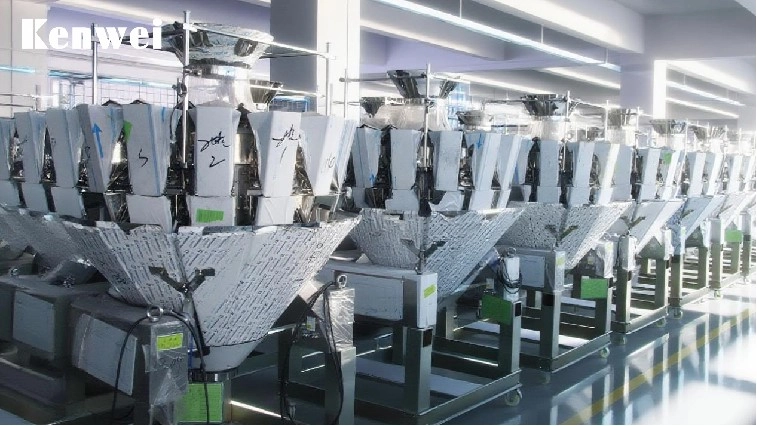
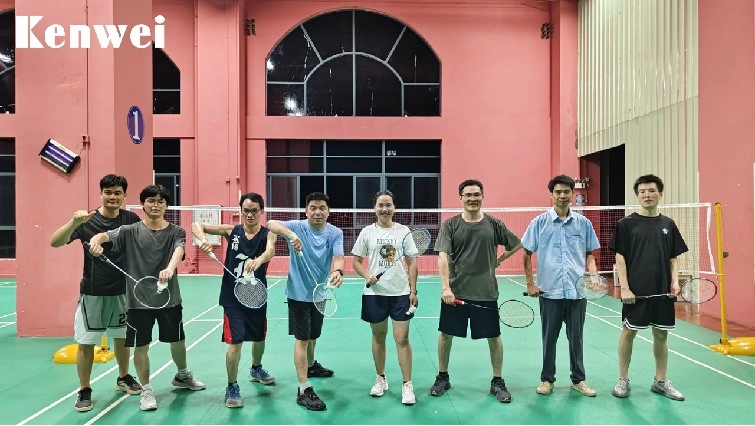
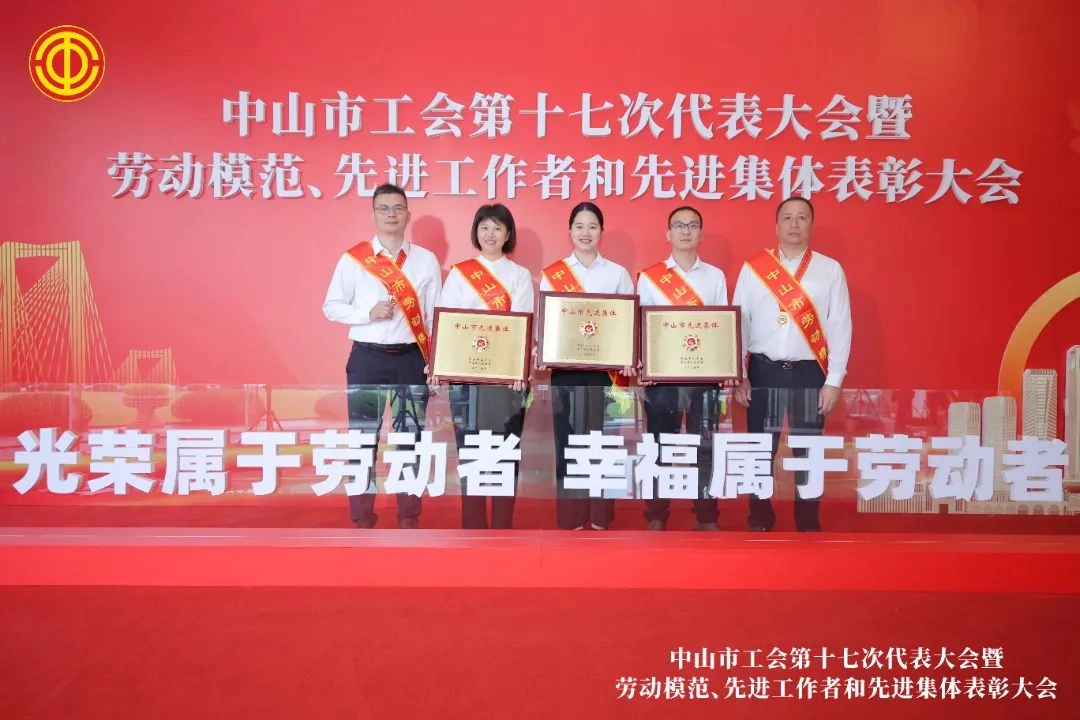
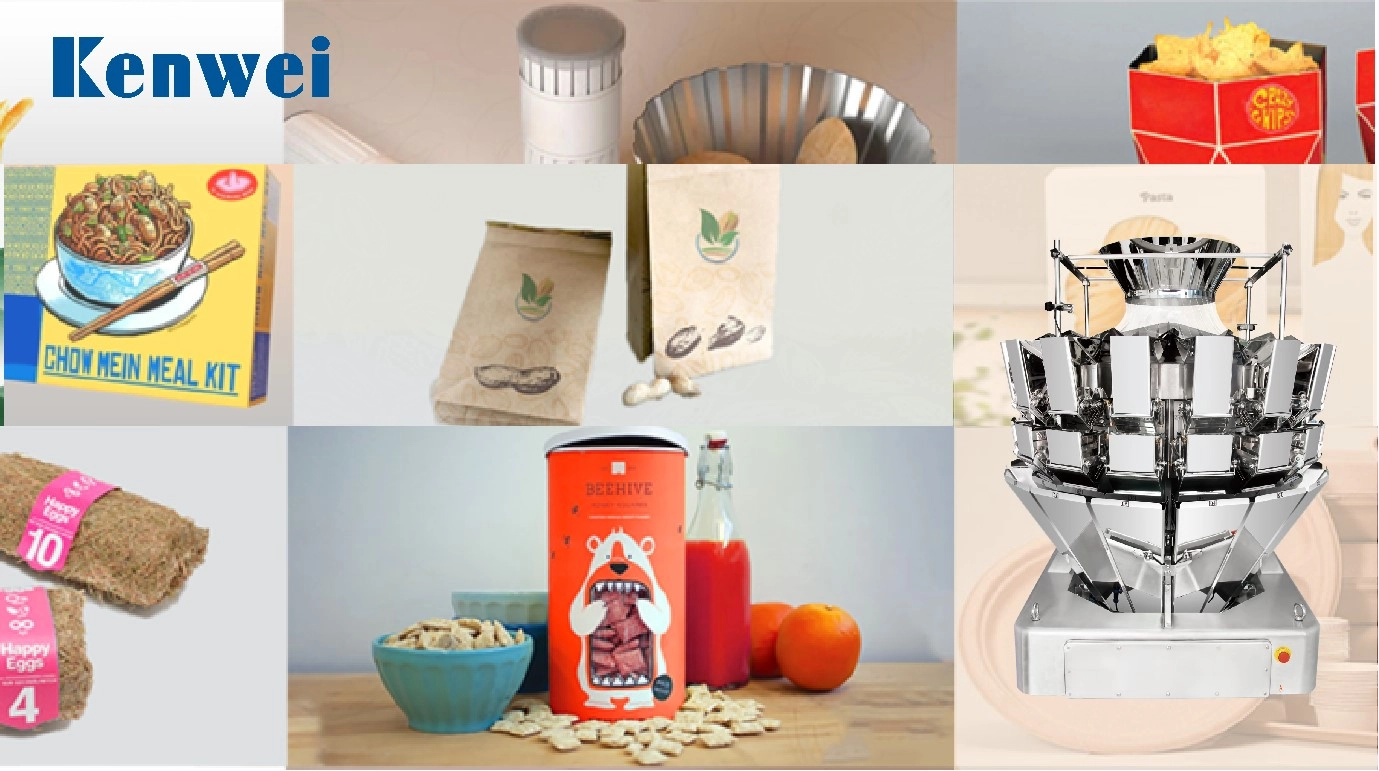
About Cooperation Process
How does Kenwei ensure the quality of its machines?
Kenwei has a stringent quality control system in place. Each machine is rigorously tested for precision, speed, and reliability before it is shipped.
About Solution suggestions
How do Kenwei’s machines improve my production efficiency?
Kenwei machines enhance efficiency by automating the weighing, packaging, and quality control processes. Our high-speed, high-precision machines ensure accurate measurements, reduce human error, and increase throughput, leading to faster production times and lower operational costs.
About Product choice
How do I choose the right product for my business?
Choosing the right machine depends on several factors:
Product Type: Different machines are suited for different products (e.g., powder, granules, etc.).
Production Capacity: Consider the volume of products you need to process and the speed requirements.
Customization: If you have specific needs, such as the need for unique features or sizes, we offer customization options.
About Price and payment
Can I get a detailed quote before making a purchase?
Absolutely! We provide detailed quotes that break down the costs for the machines, customization, shipping, and any additional services. Please contact our sales team with your requirements to receive a customized quote.
About products customization
How do I request a custom-built Kenwei machine?
To request a customized machine, simply contact our sales or engineering team.
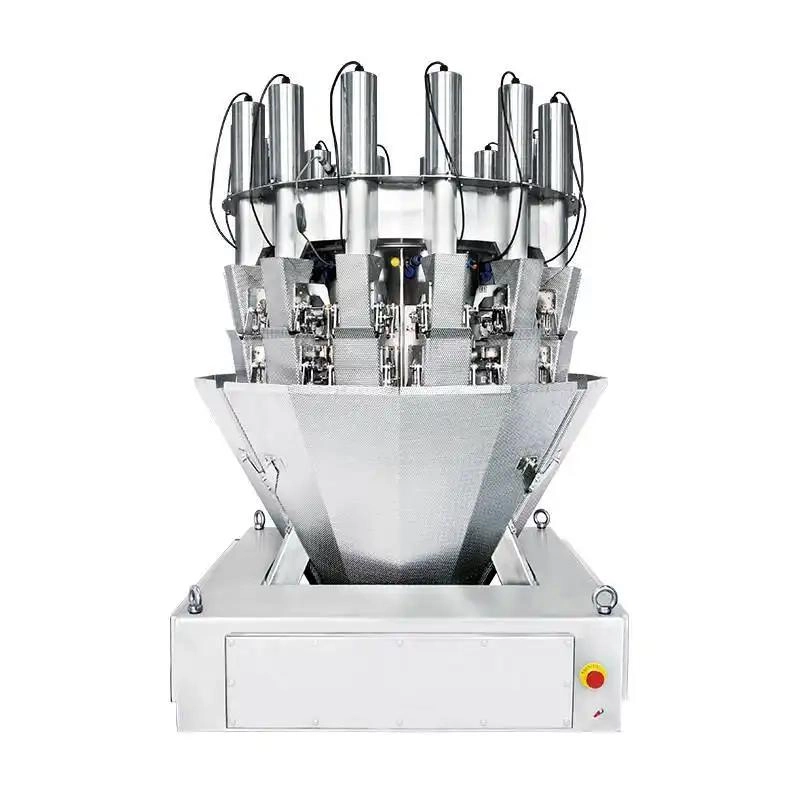
This type of weigher is designed to handle the unique characteristics of pickles, ensuring precise measurements for packaging and distribution. It uses a vertical single screw mechanism to feed the pickles into the weighing system, allowing for efficient and consistent weighing. This technology is particularly useful in food processing and packaging facilities where precise portioning is essential for quality control and customer satisfaction. This specialized equipment is perfect for accurately measuring and dispensing pickles in a production line or packaging facility. The vertical design allows for efficient and precise filling of containers, while the single screw feeding mechanism ensures consistent and reliable weighing.
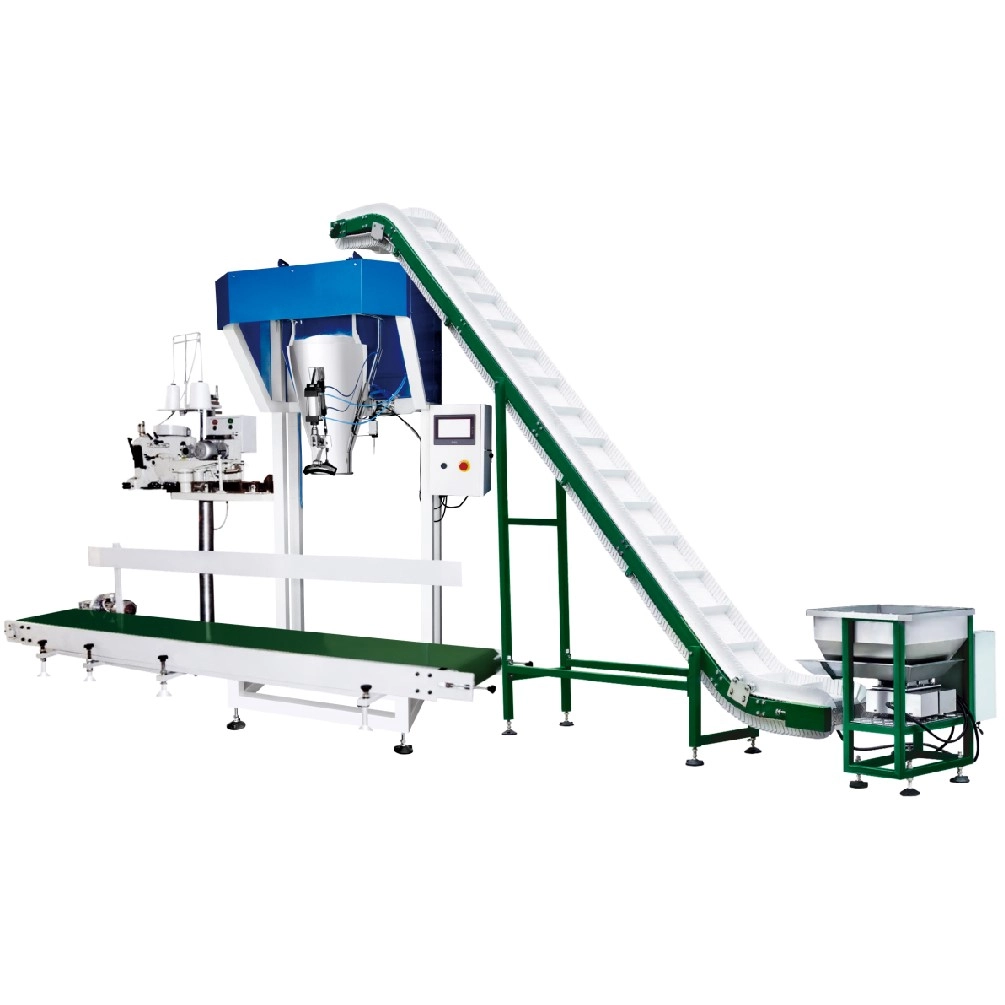
The Kenwei JW-B22 Precision Food Packaging Machine with Single Head Bulk Linear Weigher is designed for heavy-duty weighing up to 50kg. It automates feeding, weighing, bag sewing, and output for maximum efficiency. Ideal for grains like corn, rice, soybeans, barley, and wheat, it ensures high accuracy and reliability for the food, chemical, and light industries, making it the top choice for bulk grain packaging.

The JW-B13 Standard Pre-Made Bag Packing Machine is an advanced weighing and packing system ideal for granules, slices, and irregular products like snacks, nuts, pet food, and hardware. This fully automated line includes a vibrator feeder, Z conveyor, working platform, multihead weigher, and horizontal packing machine. It ensures high weighing accuracy, fast packing speed, and premium bagging quality—perfect for efficient, stable, and precise packaging.

The Kenwei JW-B16 Two Outlet Semi-Auto Sugar Weighing and Packaging Machine delivers high-precision, automated weighing for granules, slices, and irregular products like candy, coffee beans, and pet food. With a compact, cost-effective design and excellent price-performance ratio, it supports unique bag types and boosts efficiency. Optional add-ons like check weighers, metal detectors, and conveyors ensure quality control and seamless integration. Ideal for food and hardware industries.
Contact Kenwei
Our company is located in areas with convenient transportation and developed economy. Our products are supplied in a timely manner. In the course of business operation, we always focus on customers.Have any questions or concerns about our products? Please leave us a message here, and our team will get back to you promptly.
Kenwei
Kenwei
Kenwei multi weigh
Kenwei
Kenwei
Kenwei